Finnish Researchers Develop Biodegradable Plastic Substitute Made From Spider Silk
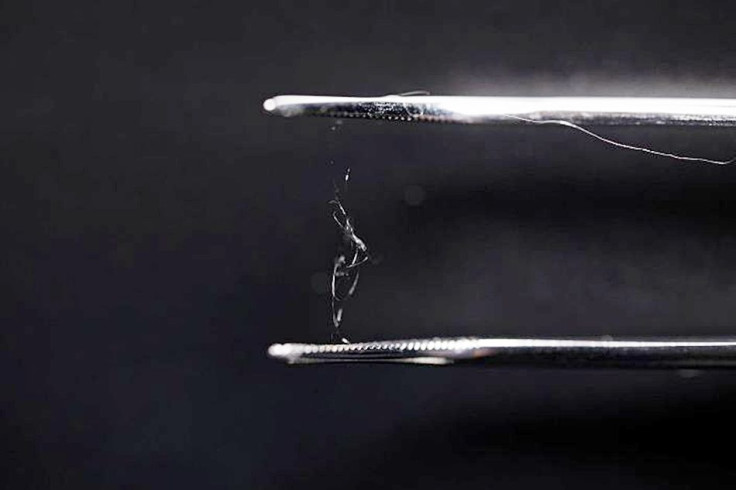
The world is choking in plastic pollution. Between five to 13 million metric tons of plastic is ditched into the oceans each year and this staggering total goes on unabated.
Put in another way, people are dumping so much plastic into the oceans and seas that we might one day reach a point where there's one pound of plastic for every three pounds of fish. While most plastic trash winds up in landfills worldwide, the decomposing plastic remnants will eventually leach into the oceans.
Scientists estimate 79 percent of the world's plastic trash is accumulating in landfills. If present trends persist, there will be 12 billion metric tons of plastic in landfills by 2050.
Clearly, this is intolerable and solutions to plastic pollution have to be found.
Researchers in Finland are on to a plastic alternative made from naturally recyclable materials. This promising new material now under development is combined wood fibers and spider silk into a new material with much of the advantages of plastic and none of the disadvantages. It might one day rival plastic in its ubiquity.
Tests have shown this unique material -- which hasn't been given a name yet -- outperforms most of today's synthetic and natural materials, including plastic. This plastic substitute exhibits high strength and stiffness combined with increased toughness and naturally decays over time.
Researchers at Aalto University and VTT Technical Research Center, both in Finland, have succeeded in overcoming the tough challenge of achieving strength and extensibility. Incorporating both these qualities into a new material has proven difficult to overcome for materials engineers because increasing strength has meant losing extensibility. The reverse is also true.
Inspired by nature, Finnish researchers developed a truly new bio-based material without the pollution hazards posed by plastic. They glued together wood cellulose fibers and the incredibly strong silk protein found in spider web threads.
The result of this process is a very firm and resilient material that might be used as a possible replacement for plastic in the future. This new material could also be used in medical applications and surgical fibers. It will also find utility in the textile and packaging industries.
Finnish researchers used birch tree pulp, broke it down to cellulose nanofibrils and aligned them into a stiff scaffold, said Pezhman Mohammadi, a research scientist from VTT. The research team also infiltrated the cellulosic network with a soft and energy-dissipating spider silk adhesive matrix.
Silk is a natural protein excreted by animals like silkworms. It's also found in spider web threads. The spider web silk used by Aalto University researchers wasn’t taken from spider webs but were instead produced by using bacteria with synthetic DNA.
"Because we know the structure of the DNA, we can copy it and use this to manufacture silk protein molecules which are chemically similar to those found in spider web threads. The DNA has all this information contained in it," according to Markus Linder, a professor at Aalto University .
Linder also said nature offers great ingredients for developing new materials. These materials include firm and easily-available cellulose and tough and flexible silk used in the research. The advantage with both of these materials is they're biodegradable and don't damage nature the same way micro-plastics and plastics do.
"Our researchers just need to be able to reproduce these natural properties." Linder added.
Pezhman said their work illustrates the new and versatile possibilities of protein engineering.
"In the future, we could manufacture similar composites with slightly different building blocks and achieve a different set of characteristics for other applications. Currently we are working on making new composite materials as implants, impact resistance objects and other products."
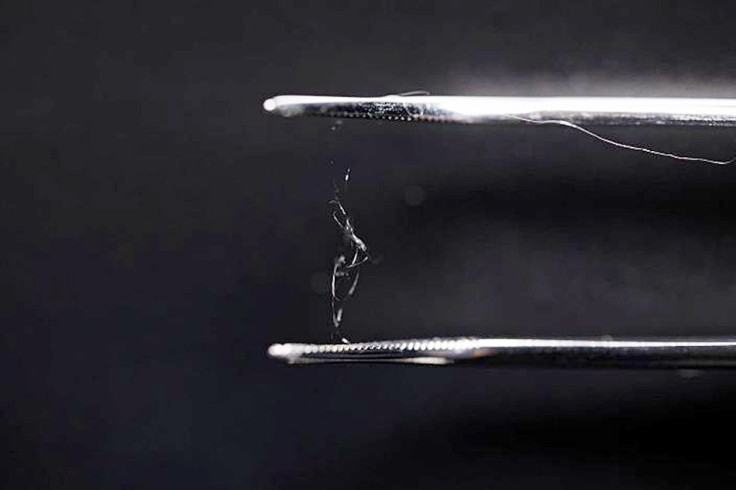