Researchers Invent Tiny Muscles with Strength of an Elephant Trunk
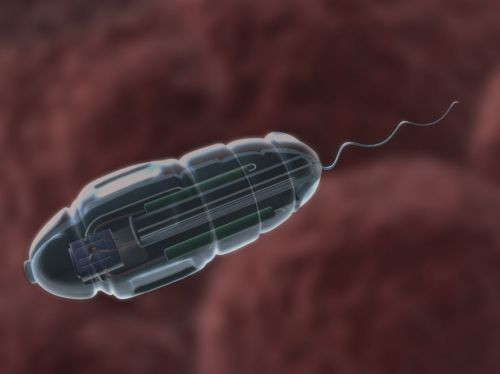
Researchers at the University of British Columbia invented tiny, flexible, rotating muscles that have the strength of an elephants trunk or octopus limbs.
The new artificial muscles are strong enough to rotate objects a thousand times their own weight.
Using extremely strong, tough, and highly flexible yarns of carbon nanotubes, the researchers developed artificial muscles that can rotate 250 degrees per millimeter of muscle length, a thousand times more than that of available artificial muscles, which are based on ferroelectrics, shape memory alloys, or conducting organic polymers, a class of materials that can hold both positive and negative electric charges, even in the absence of voltage.
A team of scientists and engineers from the University of British Columbia, the University of Wollongong in Australia, the University of Texas at Dallas and Hanyang University in Korea detailed their innovation.
The new material was conceived at the University of Texas in Dallas and then tested as an artificial muscle in Madden’s lab at UBC. Guided by theory at UBC and further experiments in Wollongong and Texas, the team was able to extract considerable torsion and power from the yarns.
“What’s amazing is that these barely visible yarns composed of fibers 10,000 times thinner than a human hair can move and rapidly rotate objects two thousand times their own weight,” said Assoc. Prof. John Madden, UBC Dept. of Electrical and Computer Engineering.
How does it work?
Well, there have been numerous demonstrations of artificial muscles in the past. The artificial muscles are materials that change their shape or size when stimulated, by heat or electricity.
“Mainly these materials either produce a bending motion or simply shrink and expand - like real muscle. What we have done, that is new, is to develop a material that produces a rotating action,” said Professor Geof Spinks of the University of Wollongong, who led the team on this research project.
The rotation occurs when the material is immersed in a liquid and a voltage is applied. The voltage causes the material to absorb some of the liquid, which causes it to twist.
“Our materials are actually thin threads of twisted carbon nanotubes. The carbon nanotubes are hollow cylinders made entirely of carbon atoms. Many millions of these tiny nanotubes are twisted together to form the fibers that we use for the torsional muscle,” said Spinks.
“In fact, it is the helically twisted nature of the carbon nanotubes that causes the rotation,” he said.
Spinks explained that the fiber partially untwists as it absorbs some liquid and swells, so one end of the fiber rotates when the end is clamped.
What will it be used for?
These extremely strong and barely visible yarns, with more research, can potentially be used to push tiny nanobots along the human body to help doctors diagnose and treat medical conditions.
“We have shown that the rotating action can be used as a mixer for fluids,” said Spinks.
“Making tiny mixers is difficult and it may be possible to use our thin threads as mixers for "lab-on-a-chip" diagnostic systems. We are also interested in pursuing other applications. One far-off application may be to use the twisting fibers to propel micro-robots in a similar way to flagella driven bacteria,” he said.
The new artificial muscles can potentially open up new doors for future researchers to put new and improved “artificial muscles” to medical use.
“While not large enough to drive an arm or power a car, this new generation of artificial muscles – which are simple and inexpensive to make – could be used to make tiny valves, positioners, pumps, stirrers and flagella for use in drug discovery, precision assembly and perhaps even to propel tiny objects inside the bloodstream,” said Madden.
“The types of rotating actuators that we are talking about here may not have direct medical uses. However, we are also working on different types of materials that we hope will be used for medical conditions,” said Spinks.
Nanorobots are thought to potentially fight off diseases in the human body, however they needed something small enough and strong enough to propel them throughout the bloodstream, and these tiny, flexible, and strong muscles, may just bring us one step closer into doing that.
“We are working on a bending type actuator that may help surgeons to insert the cochlear implant into patients. Also, we are developing an actuating sleeve that will hopefully provide relief to sufferers of lymphodema,” said Spinks.