Synthetic Implants That Help Injured Bones Regrow May Someday Be A Reality
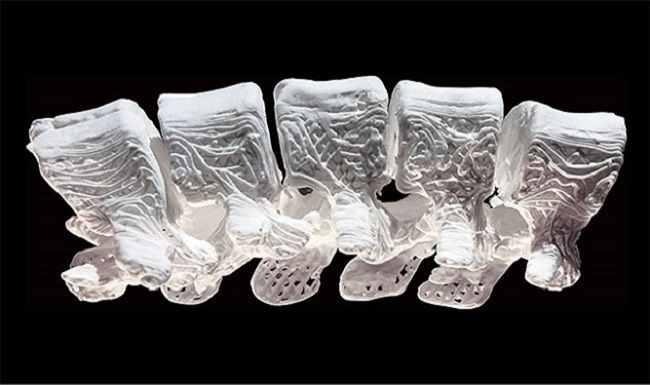
It sounds like something out of the latest Marvel film — 3D-printed technology that not only acts as a temporary replacement for missing bone, but which actually helps the bone regenerate. According to a team of researchers at Northwestern University, though, that technology may be a reality sooner than we think.
The team, led by Dr. Ramille N. Shah, has developed a custom-made ink that can be used to create what they’ve dubbed a hyperelastic “bone” implant. This implant is designed to encourage stem cells to grow in and around themselves, steadily replacing the implant with natural bone. In lab experiments with human stem cells and a variety of animals, the implant did just that, all without causing any wayward side-effects or inadvertently triggering the immune system. The team’s findings from these early trials were published late September in Science Translational Medicine.
“Its effectiveness, fast, easy synthesis, and ease of use in surgery set it apart from many of the materials now available for bone repair,” concluded the authors.
The implant is mostly made with something already commonly found in the human body, a form of the mineral calcium called hydroxyapatite. Researchers have long known that hydroxyapatite can trigger bone regeneration, but current efforts to use it as the building block of an implant have been underwhelming. By its lonesome, hydroxyapatite is brittle and hard, and scientists have compensated for this by mixing it with a widely used biodegradable polymer — a compromise that has weakened hydroxyapatite’s regenerative power. Unlike previous designs, however, the Northwestern team was able to create a material with a much higher hydroxyapatite content (90 percent) while still keeping it porous and flexible.
“Porosity is huge when it comes to tissue regeneration, because you want cells and blood vessels to infiltrate the scaffold,” Shah said in a statement announcing their findings. “Our 3-D structure has different levels of porosity that is advantageous for its physical and biological properties.”
The adaptability of the material may even allow for greater customization in the future, Shah explained.
“We can incorporate antibiotics to reduce the possibility of infection after surgery,” she said. “We also can combine the ink with different types of growth factors, if needed, to further enhance regeneration. It’s really a multi-functional material.”
Of course, it will be quite some time before any of these possibilities come to fruition. But should the team’s research continue to forge ahead, it may someday mean a great deal for accident victims, cancer survivors, and other people afflicted by degenerative bone diseases — especially if and when 3D printers become a medical mainstay within hospitals and clinics.
“The turnaround time for an implant that’s specialized for a customer could be within 24 hours,” Shah said. “That could change the world of craniofacial and orthopaedic surgery, and, I hope, will improve patient outcomes.”
Source: Jakus A, Rutz A, Jordan S, et al. Hyperelastic “bone”: A highly versatile, growth factor–free, osteoregenerative, scalable, and surgically friendly biomaterial. Science Translational Medicine. 2016.