3-D Printing Artificial Bone; Design Yields Metamaterial 20 Times Tougher
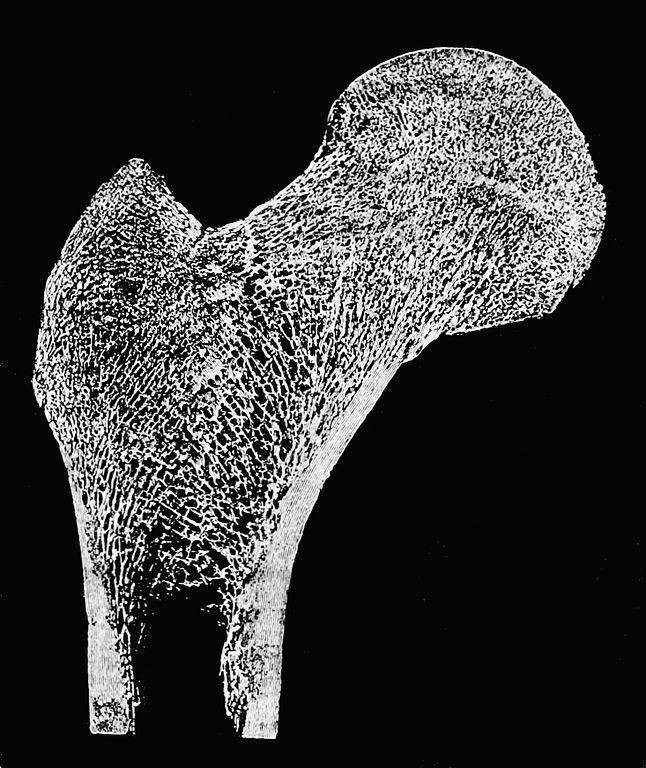
Using a combination of computer-optimized designs and synthetic materials, engineers have pushed the 3-D printing revolution further by creating artificial bone, a composite that is over 20 times more resistant to fracture than its individual materials.
Markus Buehler of the Department of Civil and Environmental Engineering at the Massachusetts Institute of Technology and his team of researchers shared their results in the journal Advanced Functional Materials.
Printing synthetic bone is remarkable since researchers used a 3-D printer capable of using two synthetic polymers in an optimized geometric pattern. Thus far, many of the achievements in 3-D printing have relied on only one polymer, a severe limitation. In the search for new durable and lightweight materials, researchers have looked to natural composites, such as bone and pearl, for inspiration.
Bone is complex; its structure long eluding engineers. It's composed mainly of two materials: a soft stretch collagen matrix that serves as a skeleton to hydroxyapatite, a hard and brittle mineral. Often thought of as a static structure, human bones are in a state of flux, constantly being dismantled and rebuilt, depending on mechanical stress and the body's mineral demand.
Nature granted bone a sophisticated design that proved difficult to emulate in a laboratory. Bone's formation is in hierarchal layers, with structure that varies at each level. Cortical bone, the solid that forms the outside of shafts, consists of bundles of concentric bone layers, each containing a microscopic canal. Trabecular bone, also known as spongy bone, appears to be a chaotic mesh upon close inspection, but is structurally optimized to bear weight.
The resulting metamaterial consists of three composite materials, each built much like brick-and-mortar walls, consisting of both a flexible skeletal structure filled with brittle materials designed to mimic the toughness associated with bone. Engineers designed composite structures that combined naturally occurring patterns found in bone and ones optimized through computer simulation. The effect of the hierarchal structure proved to be significant, with one composite proving to be 22 times more fracture resistant than one of its individual materials.
Researchers put different composite designs to the test to see if they could withstand stress and fracture similarly to bone. The computer-optimized bonelike materials were the most resistant to fracture.
"Most importantly, the experiments confirmed the computational prediction of the bonelike specimen exhibiting the largest fracture resistance," said graduate student Leon Dimas, who is the first author of the paper.
Printing 3-D structures using a combination of polymers could have a range of applications, from artificial bone grafts to printing entire buildings, brick by brick.
"As engineers we are no longer limited to the natural patterns. We can design our own, which may perform even better than the ones that already exist," Buehler said.
Souce: Dimas LS, Bratzel, GH, Eylon I, Buehler MJ. Tough Composites Inspired by Mineralized Natural Materials: Computation, 3D printing, and Testing. Advanced Functional Materials. 2013.